LT133 - Engine Pulley Removal
beat_michigan
14 years ago
Related Stories
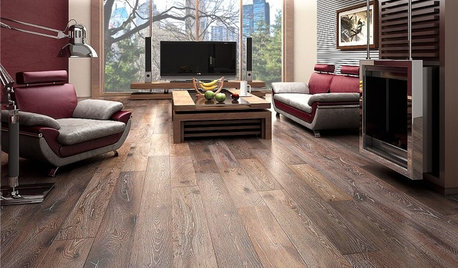
REMODELING GUIDESWhen to Use Engineered Wood Floors
See why an engineered wood floor could be your best choice (and no one will know but you)
Full Story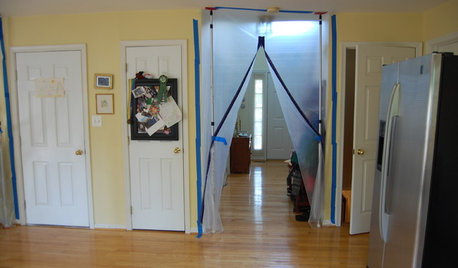
HEALTHY HOMEWhat to Know About Controlling Dust During Remodeling
You can't eliminate dust during construction, but there are ways to contain and remove as much of it as possible
Full Story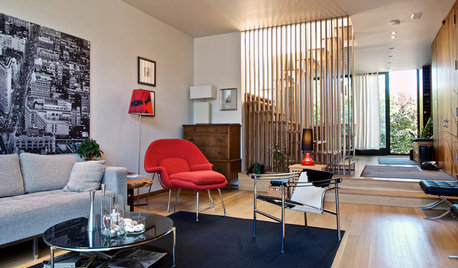
HOUZZ TOURSMy Houzz: Polished Urban Sanctuary in Toronto
Suited perfectly to its working-class downtown neighborhood, an engineer's modern home is an airy and spacious retreat
Full Story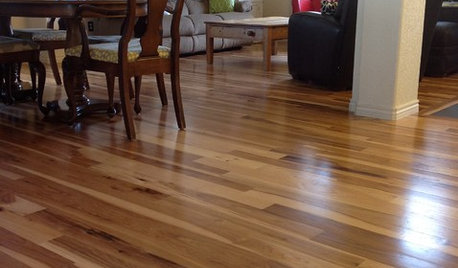
MATERIALSWhat to Ask Before Choosing a Hardwood Floor
We give you the details on cost, installation, wood varieties and more to help you pick the right hardwood flooring
Full Story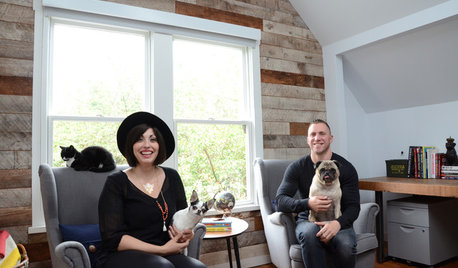
HOUZZ TOURSMy Houzz: Personal Touches Keep Things Fun in a Historic Vancouver Home
DIY updates and bold patterns help transform an 1898 Victorian
Full Story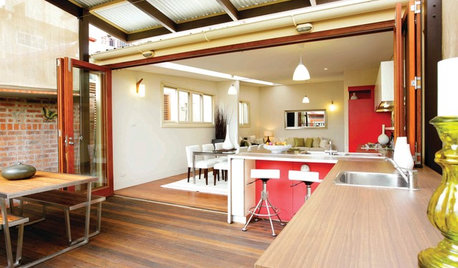
HOUZZ TOURSHouzz Tour: Way-Out-There Modern Living in Sydney
A third of its innovative kitchen is outdoors, but this modern home's indoor-outdoor connection doesn't stop there
Full Story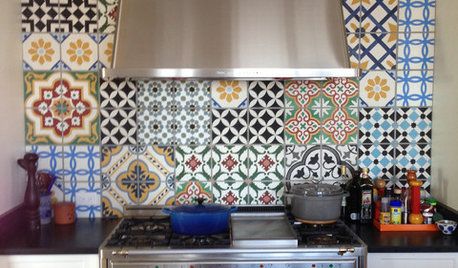
TILESo Many Reasons to Love Cement Tiles
You’ll notice their beautiful patterns right away, but cement tiles have less obvious advantages too
Full Story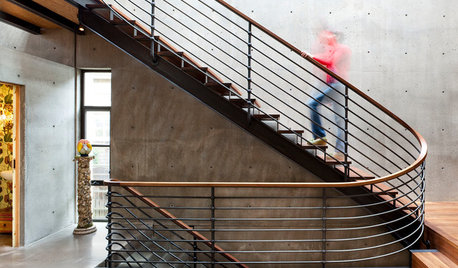
REMODELING GUIDESKey Measurements for a Heavenly Stairway
Learn what heights, widths and configurations make stairs the most functional and comfortable to use
Full Story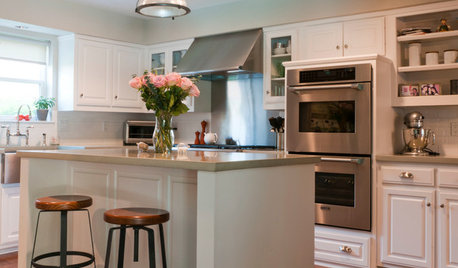
KITCHEN DESIGNShow Us Your Fabulous DIY Kitchen
Did you do a great job when you did it yourself? We want to see and hear about it
Full Story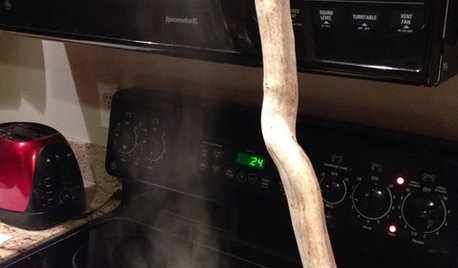
LIFEHouzz Call: Show Us Your Nutty Home Fixes
If you've masterminded a solution — silly or ingenious — to a home issue, we want to know
Full StoryMore Discussions
mownie
mownie
Related Professionals
West Chester Landscape Architects & Landscape Designers · Battle Ground Landscape Contractors · Commack Landscape Contractors · East Patchogue Landscape Contractors · El Segundo Landscape Contractors · Federal Way Landscape Contractors · Lake Worth Landscape Contractors · New Cassel Landscape Contractors · North Potomac Landscape Contractors · Oak Harbor Landscape Contractors · Palos Hills Landscape Contractors · Richmond Window Contractors · Trinity Window Contractors · University Window Contractors · Westchester Window Contractorswindcatcher
J$hort
upup_and_away
J$hort
upup_and_away
J$hort
HU-696182683